당신은 주제를 찾고 있습니까 “smt pcb & nepcon korea 2019 – Quy trình sản xuất SMT – SMT PCB Assembly Process“? 다음 카테고리의 웹사이트 https://you.tfvp.org 에서 귀하의 모든 질문에 답변해 드립니다: https://you.tfvp.org/blog/. 바로 아래에서 답을 찾을 수 있습니다. 작성자 DTD SMT 이(가) 작성한 기사에는 조회수 836회 및 좋아요 22개 개의 좋아요가 있습니다.
smt pcb & nepcon korea 2019 주제에 대한 동영상 보기
여기에서 이 주제에 대한 비디오를 시청하십시오. 주의 깊게 살펴보고 읽고 있는 내용에 대한 피드백을 제공하세요!
d여기에서 Quy trình sản xuất SMT – SMT PCB Assembly Process – smt pcb & nepcon korea 2019 주제에 대한 세부정보를 참조하세요
#smt#smtprocess#smd
Quy trình sản xuất SMT – SMT PCB Assembly Process
Công nghệ SMT là một thuật ngữ phổ biến trong ngành sản xuất bảng mạch điện tử, dây chuyền lắp ráp linh kiện điện tử.
Công nghệ SMT được phát triển vào những năm 1960 và được áp dụng một cách rộng rãi vào cuối những năm 1980. Tập đoàn IBM của Mỹ có thể được coi là người đi tiên phong trong việc ứng dụng công nghệ này. Công nghệ gắn kết bề mặt được phát triển vào những năm 1960. Đến năm 1986, các linh kiện gắn trên bề mặt chiếm nhiều nhất 10% thị trường, nhưng đã nhanh chóng trở nên phổ biến. Vào cuối những năm 1990, phần lớn các cụm mạch in điện tử công nghệ cao bị chi phối bởi các thiết bị gắn kết bề mặt.
SMT là cụm từ viết tắt của công nghệ Surface Mount Technology – gắn kết bề mặt. Đây là một phương pháp chế tạo bảng mạch phổ biến hiện nay trong các nhà máy sản xuất bảng mạch với các dây chuyền lắp ráp linh kiện điện tử tự động, bán tự động. Trong đó các thành phần điện, linh kiện điện tử được gắn trực tiếp lên bề mặt của bảng mạch in (PCB). Đây là công nghệ cốt lõi của dây chuyền lắp ráp linh kiện điện tử hiện nay.
Các công đoạn có thể được thực hiện qua một, một số máy tự động hoặc cả một dây chuyền lắp ráp linh kiện bảng mạch điện tử để tạo ra sản phẩm hoàn thiện. Ngày nay quy trình vận hành của máy SMT bảo đảm cho việc pick (gắp linh kiện điện tử lên khỏi vị trí từ băng tải cấp phôi, phễu rung, thanh rung cấp liệu, khay chứa…) và place (đặt vào vị trí trên bảng mạch in) được thực hiện với sai số nhỏ, độ chính xác cao.
Quy trình lắp ráp bảng mạch điện tử PCB trải qua các bước:
1. Chuẩn bị vật chất và kiểm tra(Material preparation and examination)
Chuẩn bị SMC và PCB và kiểm tra nếu có bất kỳ sai sót nào. PCB thường có các miếng đồng phẳng, thường là thiếc-chì, bạc hoặc vàng, không có lỗ, được gọi là miếng hàn .
2. Chuẩn bị stencil (Stencil preparation)
Stencil được sử dụng để cung cấp vị trí cố định cho quá trình in dán hàn. Nó được sản xuất theo vị trí được thiết kế của miếng hàn trên PCB.
3. Dán thiếc hàn (Solder paste printing)
Keo hàn, thường là hỗn hợp của chất trợ dung và thiếc , được sử dụng để kết nối SMC và miếng hàn trên PCB. Nó được áp dụng cho PCB với stencil bằng cách sử dụng chổi cao su trên một phạm vi góc từ 45 °-60 °.
4. Dán SMC (SMC placement)
PCB được in sau đó được chuyển đến các máy chọn và đặt , nơi chúng được đưa lên băng chuyền và các thành phần điện tử được đặt trên đó.
5. Hàn lại (Reflow soldering)
Buống sấy hàn(Soldering oven): sau khi SMC được đặt vào vị trí, các bo mạch được chuyển vào lò sấy hàn nóng chảy lại.
Vùng nhiệt sơ bộ(Pre-heat zone): vùng đầu tiên trong lò ủ là vùng nhiệt sơ bộ, nơi nhiệt độ của bo mạch và tất cả các thành phần được nâng lên đồng thời và dần dần. Tốc độ tăng nhiệt độ trong phần này là 1,0 ℃ -2,0 ℃ mỗi giây cho đến khi đạt 140 ℃ -160 ℃.
Vùng ngâm (Soak zone): bo mạch sẽ được giữ trong vùng này ở nhiệt độ từ 140 ℃ -160 ℃ trong 60-90 giây.
Khu vực chảy lại (Reflow zone): các bo mạch sau đó đi vào một vùng mà nhiệt độ tăng lên ở mức 1,0 ℃ -2,0 ℃ mỗi giây đến đỉnh 210 ℃ -230 ℃ để làm tan chảy thiếc trong bột hàn, liên kết thành phần dẫn đến các miếng đệm trên PCB . Sức căng bề mặt của vật hàn nóng chảy giúp giữ cho các thành phần ở đúng vị trí.
Vùng làm mát(Cooling zone): một phần để đảm bảo chất hàn đông cứng khi thoát ra khỏi vùng gia nhiệt để tránh lỗi mối nối .
Nếu bảng mạch là hai mặt thì quá trình in, đặt, chỉnh lại này có thể được lặp lại bằng cách sử dụng hồ hàn hoặc keo để giữ các thành phần tại chỗ.
6. Làm sạch và kiểm tra (Clean and inspection)
Làm sạch các bo mạch sau khi hàn và kiểm tra xem có bất kỳ sai sót nào không. Làm lại hoặc sửa chữa các khiếm khuyết và bảo quản sản phẩm. Các thiết bị phổ biến liên quan đến SMT bao gồm ống kính phóng đại, AOI (Kiểm tra quang học tự động), máy kiểm tra đầu dò, máy chụp X-quang, v.v.
Nguồn: cncvina.com.vn
smt pcb & nepcon korea 2019 주제에 대한 자세한 내용은 여기를 참조하세요.
Giá đựng bảng mạch SMT | PCB magazine rack – Quangminhist
Giá đựng bảng mạch SMT | PCB magazine rack tên tiếng Anh là PCB Magazine Rack chất lượng cao – giá rẻ – miễn phí vận chuyển toàn quốc. Nhận báo giá Giá đựng …
Source: quangminhist.com
Date Published: 2/25/2022
View: 2915
Tìm Hiểu Chi Tiết Về Công Nghệ Dán Bề Mặt SMT – Lidinco
Viết tắt của surface-mount equipment. PCB, PCB là bảng mạch in. Viết tắt của từ printed circuit board. Quy Trình SMT Bao Gồm Các Giai Đoạn Nào …
Source: lidinco.com
Date Published: 10/29/2021
View: 4335
주제와 관련된 이미지 smt pcb & nepcon korea 2019
주제와 관련된 더 많은 사진을 참조하십시오 Quy trình sản xuất SMT – SMT PCB Assembly Process. 댓글에서 더 많은 관련 이미지를 보거나 필요한 경우 더 많은 관련 기사를 볼 수 있습니다.
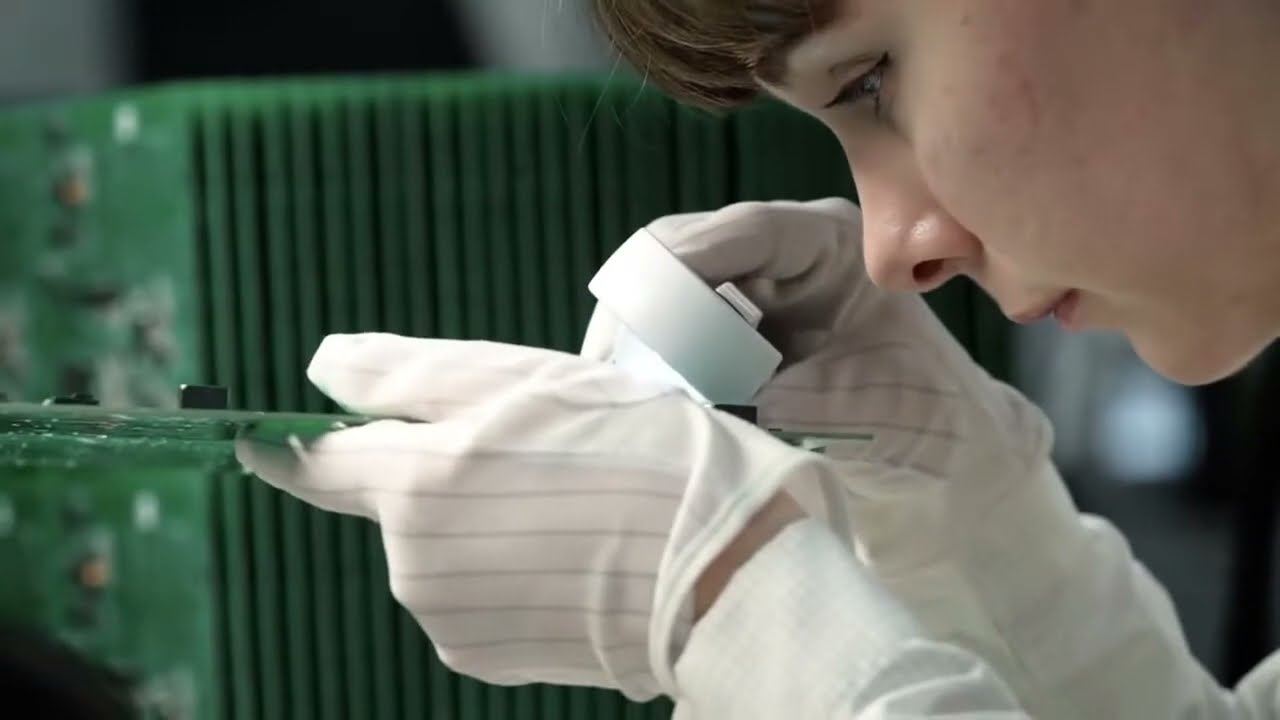
주제에 대한 기사 평가 smt pcb & nepcon korea 2019
- Author: DTD SMT
- Views: 조회수 836회
- Likes: 좋아요 22개
- Date Published: 2021. 12. 8.
- Video Url link: https://www.youtube.com/watch?v=AB2NycNjPCY
Surface-mount technology
Method for producing electronic circuits
Surface-mount components on a USB flash drive ‘s circuit board. The small rectangular chips with numbers are resistors, while the unmarked small rectangular chips are capacitors. The capacitors and resistors pictured are 0603 (1608 metric) package sizes, along with a very slightly larger 0805 (2012 metric) ferrite bead
MOSFET transistor , placed upon a British postage stamp for size comparison.
Surface-mount technology (SMT) is a method in which the electrical components are mounted directly onto the surface of a printed circuit board (PCB). An electrical component mounted in this manner is referred to as a surface-mount device (SMD). In industry, this approach has largely replaced the through-hole technology construction method of fitting components, in large part because SMT allows for increased manufacturing automation which reduces cost and improves quality. It also allows for more components to fit on a given area of substrate. Both technologies can be used on the same board, with the through-hole technology often used for components not suitable for surface mounting such as large transformers and heat-sinked power semiconductors.
An SMT component is usually smaller than its through-hole counterpart because it has either smaller leads or no leads at all. It may have short pins or leads of various styles, flat contacts, a matrix of solder balls (BGAs), or terminations on the body of the component.
History [ edit ]
Surface mounting was originally called “planar mounting”.[1]
Surface-mount technology was developed in the 1960s. By 1986 surface mounted components accounted for 10% of the market at most, but was rapidly gaining popularity.[2] By the late 1990s, the great majority of high-tech electronic printed circuit assemblies were dominated by surface mount devices. Much of the pioneering work in this technology was done by IBM. The design approach first demonstrated by IBM in 1960 in a small-scale computer was later applied in the Launch Vehicle Digital Computer used in the Instrument Unit that guided all Saturn IB and Saturn V vehicles.[3] Components were mechanically redesigned to have small metal tabs or end caps that could be directly soldered to the surface of the PCB. Components became much smaller and component placement on both sides of a board became far more common with surface mounting than through-hole mounting, allowing much higher circuit densities and smaller circuit boards and, in turn, machines or subassemblies containing the boards.
Often the surface tension of the solder is enough to hold the parts to the board; in rare cases parts on the bottom or “second” side of the board may be secured with a dot of adhesive to keep components from dropping off inside reflow ovens if the part is above the limit of 30g per square inch of pad area.[4] Adhesive is sometimes used to hold SMT components on the bottom side of a board if a wave soldering process is used to solder both SMT and through-hole components simultaneously. Alternatively, SMT and through-hole components can be soldered on the same side of a board without adhesive if the SMT parts are first reflow-soldered, then a selective solder mask is used to prevent the solder holding those parts in place from reflowing and the parts floating away during wave soldering. Surface mounting lends itself well to a high degree of automation, reducing labor cost and greatly increasing production rates.
Conversely, SMT does not lend itself well to manual or low-automation fabrication, which is more economical and faster for one-off prototyping and small-scale production, and this is one reason why many through-hole components are still manufactured. Some SMDs can be soldered with a temperature-controlled manual soldering iron, but unfortunately, those that are very small or have too fine a lead pitch are impossible to manually solder without expensive hot-air solder reflow equipment[dubious – discuss]. SMDs can be one-quarter to one-tenth the size and weight, and one-half to one-quarter the cost of equivalent through-hole parts, but on the other hand, the costs of a certain SMT part and of an equivalent through-hole part may be quite similar, though rarely is the SMT part more expensive.
Common abbreviations [ edit ]
Different terms describe the components, technique, and machines used in manufacturing. These terms are listed in the following table:
SMp term Expanded form SMD Surface-mount devices (active, passive and electromechanical components) SMT Surface-mount technology (assembling and mounting technology) SMA Surface-mount assembly (module assembled with SMT) SMC Surface-mount components (components for SMT) SMP Surface-mount packages (SMD case forms) SME Surface-mount equipment (SMT assembling machines)
Assembly techniques [ edit ]
PCB assembly line: pick-and-place machine followed by an SMT soldering oven
Where components are to be placed, the printed circuit board normally has flat, usually tin-lead, silver, or gold plated copper pads without holes, called solder pads. Solder paste, a sticky mixture of flux and tiny solder particles, is first applied to all the solder pads with a stainless steel or nickel stencil using a screen printing process. It can also be applied by a jet-printing mechanism, similar to an inkjet printer. After pasting, the boards proceed to the pick-and-place machines, where they are placed on a conveyor belt. The components to be placed on the boards are usually delivered to the production line in either paper/plastic tapes wound on reels or plastic tubes. Some large integrated circuits are delivered in static-free trays. Numerical control pick-and-place machines remove the parts from the tapes, tubes or trays and place them on the PCB.[5]
The boards are then conveyed into the reflow soldering oven. They first enter a pre-heat zone, where the temperature of the board and all the components is gradually, uniformly raised to prevent thermal shock. The boards then enter a zone where the temperature is high enough to melt the solder particles in the solder paste, bonding the component leads to the pads on the circuit board. The surface tension of the molten solder helps keep the components in place, and if the solder pad geometries are correctly designed, surface tension automatically aligns the components on their pads.
There are a number of techniques for reflowing solder. One is to use infrared lamps; this is called infrared reflow. Another is to use a hot gas convection. Another technology which is becoming popular again is special fluorocarbon liquids with high boiling points which use a method called vapor phase reflow. Due to environmental concerns, this method was falling out of favor until lead-free legislation was introduced which requires tighter controls on soldering. At the end of 2008, convection soldering was the most popular reflow technology using either standard air or nitrogen gas. Each method has its advantages and disadvantages. With infrared reflow, the board designer must lay the board out so that short components don’t fall into the shadows of tall components. Component location is less restricted if the designer knows that vapor phase reflow or convection soldering will be used in production. Following reflow soldering, certain irregular or heat-sensitive components may be installed and soldered by hand, or in large-scale automation, by focused infrared beam (FIB) or localized convection equipment.
If the circuit board is double-sided then this printing, placement, reflow process may be repeated using either solder paste or glue to hold the components in place. If a wave soldering process is used, then the parts must be glued to the board prior to processing to prevent them from floating off when the solder paste holding them in place is melted.
After soldering, the boards may be washed to remove flux residues and any stray solder balls that could short out closely spaced component leads. Rosin flux is removed with fluorocarbon solvents, high flash point hydrocarbon solvents, or low flash solvents e.g. limonene (derived from orange peels) which require extra rinsing or drying cycles. Water-soluble fluxes are removed with deionized water and detergent, followed by an air blast to quickly remove residual water. However, most electronic assemblies are made using a “No-Clean” process where the flux residues are designed to be left on the circuit board, since they are considered harmless. This saves the cost of cleaning, speeds up the manufacturing process, and reduces waste. However, it is generally suggested to wash the assembly, even when a “No-Clean” process is used, when the application uses very high frequency clock signals (in excess of 1 GHz). Another reason to remove no-clean residues is to improve adhesion of conformal coatings and underfill materials.[6] Regardless of cleaning or not those PCBs, current industry trend suggests to carefully review a PCB assembly process where “No-Clean” is applied, since flux residues trapped under components and RF shields may affect surface insulation resistance (SIR), especially on high component density boards.[7]
Certain manufacturing standards, such as those written by the IPC – Association Connecting Electronics Industries require cleaning regardless of the solder flux type used to ensure a thoroughly clean board. Proper cleaning removes all traces of solder flux, as well as dirt and other contaminants that may be invisible to the naked eye. No-Clean or other soldering processes may leave “white residues” that, according to IPC, are acceptable “provided that these residues have been qualified and documented as benign”.[8] However, while shops conforming to IPC standard are expected to adhere to the Association’s rules on board condition, not all manufacturing facilities apply IPC standard, nor are they required to do so. Additionally, in some applications, such as low-end electronics, such stringent manufacturing methods are excessive both in expense and time required.
Finally, the boards are visually inspected for missing or misaligned components and solder bridging. If needed, they are sent to a rework station where a human operator repairs any errors. They are then usually sent to the testing stations (in-circuit testing and/or functional testing) to verify that they operate correctly.
Automated optical inspection (AOI) systems are commonly used in PCB manufacturing. This technology has proven highly efficient for process improvements and quality achievements.[9]
Advantages [ edit ]
SMD resistors in original packaging – this packaging allows for use in a mounting machine
The main advantages of SMT over the older through-hole technique are:
Smaller components.
Much higher component density (components per unit area) and many more connections per component.
Components can be placed on both sides of the circuit board.
Higher density of connections because holes do not block routing space on inner layers, nor on back-side layers if components are mounted on only one side of the PCB.
Small errors in component placement are corrected automatically as the surface tension of molten solder pulls components into alignment with solder pads. (On the other hand, through-hole components cannot be slightly misaligned, because once the leads are through the holes, the components are fully aligned and cannot move laterally out of alignment.)
Better mechanical performance under shock and vibration conditions (partly due to lower mass, and partly due to less cantilevering)
Lower resistance and inductance at the connection; consequently, fewer unwanted RF signal effects and better and more predictable high-frequency performance.
Better EMC performance (lower radiated emissions) due to the smaller radiation loop area (because of the smaller package) and the lesser lead inductance. [10]
Fewer holes need to be drilled. (Drilling PCBs is time-consuming and expensive.)
Lower initial cost and time of setting up for mass production, using automated equipment.
Simpler and faster automated assembly. Some placement machines are capable of placing more than 136,000 components per hour.
Many SMT parts cost less than equivalent through-hole parts.
Disadvantages [ edit ]
SMT may be unsuitable as the sole attachment method for components that are subject to frequent mechanical stress, such as connectors that are used to interface with external devices that are frequently attached and detached. [ citation needed ]
SMDs’ solder connections may be damaged by potting compounds going through thermal cycling.
Manual prototype assembly or component-level repair is more difficult and requires skilled operators and more expensive tools, due to the small sizes and lead spacings of many SMDs. [11] Handling of small SMT components can be difficult, requiring tweezers, unlike nearly all through-hole components. Whereas through-hole components will stay in place (under gravitational force) once inserted and can be mechanically secured prior to soldering by bending out two leads on the solder side of the board, SMDs are easily moved out of place by a touch of a soldering iron. Without developed skill, when manually soldering or desoldering a component, it is easy to accidentally reflow the solder of an adjacent SMT component and unintentionally displace it, something that is almost impossible to do with through-hole components.
Handling of small SMT components can be difficult, requiring tweezers, unlike nearly all through-hole components. Whereas through-hole components will stay in place (under gravitational force) once inserted and can be mechanically secured prior to soldering by bending out two leads on the solder side of the board, SMDs are easily moved out of place by a touch of a soldering iron. Without developed skill, when manually soldering or desoldering a component, it is easy to accidentally reflow the solder of an adjacent SMT component and unintentionally displace it, something that is almost impossible to do with through-hole components. Many types of SMT component packages cannot be installed in sockets, which provide for easy installation or exchange of components to modify a circuit and easy replacement of failed components. (Virtually all through-hole components can be socketed.)
SMDs cannot be used directly with plug-in breadboards (a quick snap-and-play prototyping tool), requiring either a custom PCB for every prototype or the mounting of the SMD upon a pin-leaded carrier. For prototyping around a specific SMD component, a less-expensive breakout board may be used. Additionally, stripboard style protoboards can be used, some of which include pads for standard sized SMD components. For prototyping, “dead bug” breadboarding can be used. [12]
Solder joint dimensions in SMT quickly become much smaller as advances are made toward ultra-fine pitch technology. The reliability of solder joints becomes more of a concern, as less and less solder is allowed for each joint. Voiding is a fault commonly associated with solder joints, especially when reflowing a solder paste in the SMT application. The presence of voids can deteriorate the joint strength and eventually lead to joint failure. [13] [14]
SMDs, usually being smaller than equivalent through-hole components, have less surface area for marking, requiring marked part ID codes or component values to be more cryptic and smaller, often requiring magnification to be read, whereas a larger through-hole component could be read and identified by the unaided eye. This is a disadvantage for prototyping, repair, rework, reverse engineering, and possibly for production set-up.
Rework [ edit ]
Defective surface-mount components can be repaired by using soldering irons (for some connections), or using a non-contact rework system. In most cases a rework system is the better choice because SMD work with a soldering iron requires considerable skill and is not always feasible.
Reworking usually corrects some type of error, either human- or machine-generated, and includes the following steps:
Melt solder and remove component(s)
Remove residual solder
Print solder paste on PCB, directly or by dispensing
Place new component and reflow.
Sometimes hundreds or thousands of the same part need to be repaired. Such errors, if due to assembly, are often caught during the process. However, a whole new level of rework arises when component failure is discovered too late, and perhaps unnoticed until the end user of the device being manufactured experiences it. Rework can also be used if products of sufficient value to justify it require revision or re-engineering, perhaps to change a single firmware-based component. Reworking in large volume requires an operation designed for that purpose.
There are essentially two non-contact soldering/desoldering methods: infrared soldering and soldering with hot gas.[15]
Infrared [ edit ]
With infrared soldering, the energy for heating up the solder joint is transmitted by long- or short-wave infrared electromagnetic radiation.
Advantages:
Easy setup
No compressed air required
No requirement for different nozzles for many component shapes and sizes, reducing cost and the need to change nozzles
Fast reaction of infrared source (depends on system used)
Disadvantages:
Central areas will be heated more than peripheral areas
Temperature control is less precise, and there may be peaks
Nearby components must be shielded from heat to prevent damage, which requires additional time for every board
Surface temperature depends on the component’s albedo: dark surfaces will be heated more than lighter surfaces
The temperature additionally depends on the surface shape. Convective loss of energy will reduce the temperature of the component
No reflow atmosphere possible
Hot gas [ edit ]
During hot gas soldering, the energy for heating up the solder joint is transmitted by a hot gas. This can be air or inert gas (nitrogen).
Advantages:
Simulating reflow oven atmosphere
Some systems allow switching between hot air and nitrogen
Standard and component-specific nozzles allow high reliability and faster processing
Allow reproducible soldering profiles
Efficient heating, large amounts of heat can be transferred
Even heating of the affected board area
Temperature of the component will never exceed the adjusted gas temperature
Rapid cooling after reflow, resulting in small-grained solder joints (depends on system used)
Disadvantages:
Thermal capacity of the heat generator results in slow reaction whereby thermal profiles can be distorted (depends on system used)
Packages [ edit ]
Example of component sizes, metric and imperial codes for two-terminal packages and comparison included
Surface-mount components are usually smaller than their counterparts with leads, and are designed to be handled by machines rather than by humans. The electronics industry has standardized package shapes and sizes (the leading standardisation body is JEDEC).
Identification [ edit ]
Resistors For 5% precision SMD resistors usually are marked with their resistance values using three digits: two significant digits and a multiplier digit. These are quite often white lettering on a black background, but other colored backgrounds and lettering can be used. For 1% precision SMD resistors, the code is used, as three digits would otherwise not convey enough information. This code consists of two digits and a letter: the digits denote the value’s position in the E96 Series of values, while the letter indicates the multiplier.[16] Capacitors Non-electrolytic capacitors are usually unmarked and the only reliable method of determining their value is removal from the circuit and subsequent measurement with a capacitance meter or impedance bridge. The materials used to fabricate the capacitors, such as nickel tantalate, possess different colours and these can give an approximate idea of the capacitance of the component.[ citation needed ] Generally physical size is proportional to capacitance and (squared) voltage for the same dielectric. For example, a 100 nF, 50 V capacitor may come in the same package as a 10 nF, 150 V device. SMD (non-electrolytic) capacitors, which are usually monolithic ceramic capacitors, exhibit the same body color on all four faces not covered by the end caps. SMD electrolytic capacitors, usually tantalum capacitors, and film capacitors are marked like resistors, with two significant figures and a multiplier in units of picofarads or pF, (10−12 farad.) Inductors Smaller inductance with moderately high current ratings are usually of the ferrite bead type. They are simply a metal conductor looped through a ferrite bead and almost the same as their through-hole versions but possess SMD end caps rather than leads. They appear dark grey and are magnetic, unlike capacitors with a similar dark grey appearance. These ferrite bead type are limited to small values in the nanohenry (nH) range and are often used as power supply rail decouplers or in high frequency parts of a circuit. Larger inductors and transformers may of course be through-hole mounted on the same board. SMT inductors with larger inductance values often have turns of wire or flat strap around the body or embedded in clear epoxy, allowing the wire or strap to be seen. Sometimes a ferrite core is present also. These higher inductance types are often limited to small current ratings, although some of the flat strap types can handle a few amps. As with capacitors, component values and identifiers for smaller inductors are not usually marked on the component itself; if not documented or printed on the PCB, measurement, usually removed from the circuit, is the only way of determining them. Larger inductors, especially wire-wound types in larger footprints, usually have the value printed on the top. For example, “330”, which equates to a value of 33 μH. Discrete semiconductors Discrete semiconductors, such as diodes and transistors are often marked with a two- or three-symbol code. The same code marked on different packages or on devices from different manufacturers can translate to different devices. Many of these codes, used because the devices are too small to be marked with more traditional numbers used on larger packages, correlate to more familiar traditional part numbers when a correlation list is consulted. GM4PMK in the United Kingdom has prepared a correlation list, and a similar .pdf list is also available, although these lists are not complete. Integrated circuits Generally, integrated circuit packages are large enough to be imprinted with the complete part number which includes the manufacturer’s specific prefix, or a significant segment of the part number and the manufacturer’s name or logo.
See also [ edit ]
SMT là gì? Tất tần tật về công nghệ SMT
Khi các thiết kế điện tử ngày nay trở nên nhỏ hơn và phức tạp hơn, nhiều kỹ sư đang dựa vào công nghệ dán bề mặt. Sau những năm 1980, công nghệ này đã trở thành công nghệ lắp ráp PCB được ưa chuộng trong sản xuất điện tử và không hề bị loại bỏ kể từ đó.
Hầu hết các thành phần của điện thoại trong túi của bạn – cho dù đó là iPhone 11 hay linh kiện lắp đặt màn hình LED như card màn hình LED được tạo ra thông qua công nghệ gắn kết bề mặt (SMT).
Vậy SMT là gì, và tại sao cần phải tạo ra công nghệ này?
Công nghệ SMT
Bằng cách sử dụng công nghệ này, bạn có thể đạt được các lắp ráp nhỏ hơn với khả năng lặp lại tuyệt vời. Tất cả điều này là do mức độ tự động hóa và độ chính xác cao đi kèm với công nghệ Surface Mount Technology. Nhiều nhà sản xuất hiện đang sử dụng công nghệ này vì nó cho phép họ thiết kế các PCB nhỏ có trọng lượng nhẹ và nhỏ gọn một cách nhanh chóng.
Tốt hơn nữa, đó là một quá trình nhanh hơn nhiều so với công nghệ xuyên lỗ. Công nghệ Surface Mount không đòi hỏi quá nhiều công việc trong quá trình lắp ráp. SMT là một quá trình đơn giản chỉ cần chọn và đặt các thành phần PCB lên bo mạch.
Đọc thêm: PCB là gì? Cấu tạo và ứng dụng thực tiễn như thế nào?
Ưu nhược điểm của công nghệ SMT
Ưu điểm
KHẢ NĂNG CHI TRẢ
Một trong những lý do khiến việc lắp ráp SMT được hình thành là để giảm chi phí sản xuất.
SMT yêu cầu phải khoan ít lỗ hơn rất nhiều trên bảng mạch. Điều này làm giảm đáng kể chi phí xử lý và xử lý.
Cuối cùng, SMT có nhiều khả năng tạo ra khối lượng lớn, cho phép chi phí trên mỗi đơn vị tốt hơn.
HIỆU QUẢ
Một lợi ích khác của lắp ráp SMT là nó sử dụng không gian bảng mạch theo cách hiệu quả hơn nhiều. Nhờ lắp ráp SMT, các kỹ sư hiện có thể biến các thiết bị điện tử phức tạp thành các cụm nhỏ hơn.
Ngoài việc sử dụng hiệu quả hơn không gian trên PCB, lắp ráp SMT nhanh hơn nhiều, cho phép các nhà sản xuất tăng tổng sản lượng. Để đặt điều này trong viễn cảnh, một cái gì đó có thể mất 1-2 giờ để thực hiện, việc lắp ráp SMT chỉ mất 10 – 15 phút.
TÍNH ĐƠN GIẢN
Trong lắp ráp xuyên lỗ, dây dẫn đi qua các lỗ để kết nối các thành phần. Vì các thành phần SMT được hàn ngay trên PCB nên cấu trúc tổng thể ít phức tạp hơn nhiều .
ÍT MẮC LỖI
Việc lắp ráp SMT phụ thuộc rất nhiều vào máy móc chứ không phụ thuộc quá nhiều vào con người. SMT là một quy trình ít bị lỗi vì nó gần như hoàn toàn tự động.
PHÁT RA BỨC XẠ THẤP
Có lẽ, một trong những ưu điểm đáng kể nhất của công nghệ SMT là phát bức xạ thấp. Khi lắp ráp các bộ phận bằng SMT, bạn sẽ gặp phải lượng bức xạ thấp. Do đó, nó có nghĩa là SMT là một phương pháp lắp ráp an toàn hơn một chút so với các phương pháp lắp ráp khác.
Nhược điểm
Như một số các quy trình sản xuất khác, công nghệ SMT có một số nhược điểm.
Điểm lớn nhất là nó đòi hỏi sự chú ý đến chi tiết cao hơn nhiều so với lắp ráp xuyên lỗ. Ngay cả với quy trình phần lớn được tự động hóa, các thông số thiết kế của bạn vẫn phải được đáp ứng để tạo ra sản phẩm cuối cùng chất lượng. Điều này phần lớn rơi vào vai của nhà thiết kế và nhà sản xuất điện tử.
Rắc rối cũng có thể phát sinh khi SMT được sử dụng để đặt các thành phần vào PCB, nó sẽ hoạt động trong các điều kiện liên quan đến:
Ứng suất cơ học
Môi trường áp lực
Căng thẳng nhiệt độ
Vấn đề này có thể được giảm thiểu bằng cách kết hợp SMT với các quy trình xuyên lỗ để có được những lợi ích của cả hai.
Quy trình chung của công nghệ SMT
In hàn dán trên bo mạch
Quá trình đầu tiên liên quan đến việc in keo hàn lên bảng. Ở đây, người sản xuất sử dụng máy in lụa. Bước này nhằm đảm bảo quá trình hàn các thành phần trên tấm đệm diễn ra tốt đẹp.
Gắn các bộ phận
Thứ hai, việc gắn các bộ phận theo sau. Việc gắn các bộ phận liên quan đến việc đặt linh kiện cẩn thận trên một PCB cố định.
Sự rắn chắc
Sau khi đặt các bộ phận, quá trình đông đặc sẽ diễn ra theo sau. Chức năng của đông đặc là làm tan chảy các chất kết dính SMT. Bằng cách này, các nhà sản xuất đảm bảo rằng các thành phần gắn kết bề mặt sẽ dính chính xác trên bo mạch. Lò đóng rắn nằm ở phía sau của máy định vị sẽ thực hiện quá trình đông đặc.
Hàn lại
Sau khi đông đặc, tiếp theo là hàn lại. Mục đích của hàn lại là để đảm bảo rằng chất hàn nóng chảy và mối nối của bo mạch PCB.
Kiểm tra quang học tự động
Bước thứ năm sau khi hàn lại là kiểm tra quang học tự động ( AOI ). Mục đích chính của AOI là kiểm tra cả chất lượng hàn và lắp ráp. Với tính năng Kiểm tra quang học tự động, có thể phát hiện lỗi đủ sớm trước khi phát hành bo mạch ra thị trường. Đó là điều cần thiết trước khi đi vào sản xuất hàng loạt bảng mạch.
Đọc thêm: AOI là gì?
Cắt ván
Sau khi kiểm tra quang học tự động, họ đang cắt bảng sau. Các nhà thiết kế cắt bảng để tạo thành một cá nhân duy nhất. Có một số phương pháp cắt bằng máy được sử dụng ở đây.
Mài bảng
Sau khi cắt ván theo hình dạng yêu cầu, ngay sau đó sẽ tiến hành mài. Nghiền là một trong những quy trình SMT thiết yếu. Vai trò chính của quá trình mài là để đảm bảo quá trình xay ra khỏi gờ. Phay ra khỏi gờ đảm bảo rằng bạn sẽ có một tấm ván mịn. Trong quá trình sản xuất bo mạch, chắc chắn bạn sẽ gặp phải các cạnh thô. Phay đảm bảo mài nhẵn các cạnh thô.
Phay bảng
Sau khi xay xát, sau đó quy trình cuối cùng tiếp theo. Quá trình cuối cùng bao gồm rửa bảng. Làm sạch bo mạch đảm bảo loại bỏ các cặn hàn có hại như chất trợ dung. Bạn có thể làm sạch bo mạch bằng tay hoặc bằng máy. Có những loại máy đặc biệt có thể giúp bạn có được kết quả làm sạch tốt nhất. May mắn thay, bạn có thể làm sạch thủ công nếu bạn không đủ khả năng mua những chiếc máy làm sạch chuyên dụng như vậy.
Sự khác biệt giữa SMT và SMD là gì?
Có một sự khác biệt đáng kể giữa SMT và SMD. Thật không may, nhiều người không hiểu sự khác biệt giữa cái này. Nếu bạn đang ở đây, hãy tự coi mình là người may mắn. Ở đây, bạn sẽ đánh giá cao sự khác biệt giữa SMT và SMD.
Với SMT, SMT (Công nghệ gắn kết bề mặt) là toàn bộ công nghệ liên quan đến việc hàn và gắn các thành phần điện tử trên bảng mạch. Các tính năng điện tử bao gồm tụ điện, điện trở và bóng bán dẫn trên PCB, chưa kể đến một số ít. Mặc dù bạn có thể đặt các miếng thủ công, nhưng hầu hết, các nhà sản xuất sử dụng máy móc đặc biệt. Với máy móc, kết quả chủ yếu là hoàn hảo và chất lượng cao.
Máy SMT đặc biệt, chủ yếu được gọi là máy Pick-and-Place, cẩn thận chọn và đặt tất cả các thành phần và đặt chúng trên bảng mạch. Một lần nữa, bạn có thể thực hiện việc này theo cách thủ công nếu bạn muốn hoặc có kinh nghiệm làm việc đó theo cách thủ công. Tuy nhiên, bạn có thể phải đi chọn và đặt máy theo yêu cầu để có kết quả tốt nhất cho sản phẩm tốt nhất cho kết quả tốt nhất.
Surface Mount Devices (SMD) là các linh kiện được nhà sản xuất gắn trên mạch điện tử để mạch hoạt động. SMT là công nghệ, trong khi SMD là các bộ phận phù hợp với bảng mạch trần. Các thành phần cơ bản phải tìm đường đến bảng bằng quy trình SMT. Hầu hết, các nhà sản xuất sẵn sàng sử dụng máy móc cạnh tranh để gắn và hàn SMD trên một bảng mạch trần.
Trong giai đoạn đầu, việc đặt các thiết bị gắn trên bề mặt chủ yếu được thực hiện bằng tay. Tuy nhiên, với công nghệ được cải tiến, máy chọn và đặt đã đảm nhận vai trò này. Những chiếc máy này hoàn hảo để chọn và đặt tất cả các bộ phận trên bảng mạch. Họ thực hiện công việc nhanh hơn và hiệu quả hơn nhiều so với việc chọn và đặt các thành phần theo cách thủ công.
Các thành phần SMT chung
Có rất nhiều thành phần thiết bị gắn kết bề mặt. Tất cả các thiết bị này hoạt động đồng bộ để tạo thành một mạch hoạt động. Một số thành phần SMD phổ biến nhất mà bạn có trên bo mạch bao gồm:
Thành phần thụ động: SMD thụ động
Hầu hết các thành phần thụ động bao gồm điện cảm, điện dung và thiết bị tổng hợp. Trên bảng mạch, các thành phần SMD thụ động chủ yếu có hình trụ và hình chữ nhật. Khối lượng của các bộ phận này cũng thấp hơn mười lần so với các bộ phận xuyên lỗ.
Bóng bán dẫn và điện trở
Các bóng bán dẫn và điện trở cũng là các thành phần SMD tiêu chuẩn. Nếu bạn quan sát xung quanh, bạn sẽ không bỏ lỡ các điện trở và bóng bán dẫn trên PCB. Điện trở phân chia điện áp, giảm dòng điện và điều chỉnh mức tín hiệu. Ngoài điện trở, bạn cũng sẽ tìm thấy các bóng bán dẫn trên PCB. Các bóng bán dẫn khuếch đại và chuyển đổi công suất điện tử và tín hiệu điện tử trên một bảng mạch in. Một bóng bán dẫn có thể hoạt động như một công tắc và một bộ khuếch đại cùng một lúc. Thời điểm không có dòng điện đến đế, thì dòng điện nhỏ sẽ chạy giữa bộ phát và bộ thu.
Diode
Bạn sẽ luôn tìm thấy diode trên bảng mạch in. Nhưng các chức năng của điốt là gì? Điốt là thiết bị hai đầu cho phép dòng điện lưu thông, nhưng chỉ theo một hướng. Chúng chủ yếu chuyển đổi Dòng điện xoay chiều (AC) thành Dòng điện một chiều (DC).
Mạch tích hợp
Các mạch tích hợp là các chip logic đơn giản. Nếu không có mạch tích hợp, bo mạch sẽ không hoạt động vì chúng giúp truyền tín hiệu và giảm nhiệt độ bo mạch.
(Các thành phần SMD phổ biến: điện trở quảng cáo bóng bán dẫn)
Ứng dụng công nghệ SMT
Công nghệ gắn kết bề mặt được sử dụng rất nhiều trong sản xuất gần như tất cả các vi mạch điện tử ngày nay. Công nghệ Surface Mount có thể sử dụng để gắn hầu hết các thành phần điện trên PCB.
Công nghệ này đóng gói nhiều linh kiện điện tử hơn vào không gian nhỏ hơn trên PCB. SMT là một công nghệ sẽ tiếp tục phát triển trong những năm tới vì nó sẽ không sớm kết thúc. Nếu bạn là một nhà lắp ráp bảng mạch in, thì cách tốt nhất là sử dụng công nghệ này. Mặc dù nó có thể khiến bạn tốn nhiều tiền hơn, nhưng SMT là một trong những công nghệ tốt nhất để sử dụng.
Gia công PCB và PCBA với công nghệ SMT tiên tiến
Thegioiic nhận gia công PCB từ 2-6 lớp (layer) với chất lượng tốt và giá cả hợp lý.
Báo PCB giá online
Sau đây là một có sản phẩm điển hình:
PCB 2 lớp phủ thiếc:
PCB 6 lớp mạ vàng:
Số lớp: 1 tới 6 lớp:
Vật liệu: FR-4, CEM-1, CEM-3, High TG, FR4 Halogen Free, Rogers
Độ dày board: 0.21mm to 7.0mm
Độ dày đồng: 0.5 OZ to 7.0 OZ
Lớp dày đồng trong lỗ: >25.0 um (>1mil)
Kích thước board:
Max. Board Size: 23 × 25 (580mm×900mm)
Min. Drilled Hole Size: 3mil (0.075mm)
Min. Line Width: 3mil (0.075mm)
Min. Line Spacing: 3mil (0.075mm)
Hoàn thiện bề mặt (Surface finishing): HASL / HASL lead free, HAL, mạ thiếc, mạ vàng, mạ bạc…
Màu phủ (Solder Mask): Xanh lá, vàng, đen, trắng, đỏ, xanh dương
Sai số:
Sai số hình dáng: ±0.13 mm
Sai số lỗ: PTH: ±0.076mm NPTH: ±0.05mm
Gia công cắm chip SMT PCBA:
Ngoài ra, Thegioiic còn nhận gia công PCBA bằng công nghệ SMT tiên tiến. Thegioiic có ưu điểm nổi bật sau:
Công nghệ máy SMT của Siemens có thể cắm được các loại IC với kiểu chân BGA và QFP, Chip 0402, linh kiện dạng ống,
Số lượng đặt hàng có thể từ 50-5000 PCBA,
Giá cả hợp lý và chất lượng tốt,
Thời gian giao hàng đúng hẹn.
Báo PCB giá online hoặc gửi email [email protected]
Máy SMT | Dây chuyền SMT | Giải pháp máy SMT tự động
Máy SMT là gì? Các thiết bị và giải pháp trong dây chuyền SMT
Máy SMT là gì?
Máy SMT (Surface mount technology) là các thiết bị được sử dụng trong lắp ráp bảng mạch PCB sử dụng công nghệ gắn bề mặt trong đó linh kiện được được gắn trực tiếp lên bề mặt của PCB.
Máy SMT (Surface mount technology)
Máy SMT được phân loại như thế nào?
Phân loại máy SMT theo ứng dụng:
– Ứng dụng gắp – đặt (Placement)
– Ứng dụng kiểm tra (Inspection)
– Ứng dụng hàn (Soldering)
– Ứng in mạch (Screen Printing)
– Ứng dụng làm sạch (Cleaning)
– Ứng dụng sửa chữa (Repair & Rework)
– Các ứng dụng khác (Other)
Phân loại máy SMT theo ngành nghề:
– Ngành điện – điện tử (Consumer Electronics)
– Ngành ô tô (Automotive)
– Ngành hàng không vũ trụ (Aerospace)
– Ngành hàng thiết yếu (Defense)
Dây chuyền SMT có những thiết bị và máy móc nào?
Dây chuyền SMT có thể được chia thành hai loại, theo mức độ tự động hóa có thể được chia thành dây chuyền SMT tự động và dây chuyền SMT bán tự động; phù hợp với quy mô của dây chuyền sản xuất có thể được chia thành dây chuyền sản xuất lớn, vừa và nhỏ. Các thiết bị trong dây chuyền SMT bao gồm: Máy nạp PCB (PCB loader), Máy in stencil tự động 9Auto smt stencil printer), băng tải PCB ( PCB converyor), máy Pick & Palce, lò lung SMT (SMT reflow oven), AOI. Ngoài ra còn có các thiết bị phụ trợ như: Thiết bị phụ trợ, thiết bị kiểm tra, thiết bị sửa chữa, thiết bị làm sạch, thiết bị sấy và thiết bị bảo quản vật liệu.
Thị trường máy SMT hiện nay
Thị trường thiết bị công nghệ gắn trên bề mặt toàn cầu – máy SMT sẽ đạt 4,5 tỷ đô la Mỹ vào năm 2027. Giữa cuộc khủng hoảng COVID-19, thị trường toàn cầu cho máy SMT ước tính đạt 3,0 tỷ đô la Mỹ vào năm 2020, dự kiến sẽ đạt quy mô 4,5 tỷ đô la Mỹ vào năm 2027, hiển thị với tốc độ CAGR là 6,2% trong giai đoạn phân tích 2020-2027.
Lựa chọn TPA là đơn vị cung cấp giải pháp về Máy SMT
TPA là đơn vị có nhiều năm kinh nghiệm trong việc cung cấp các giải pháp về sản xuất PCB cũng như giải pháp về máy SMT. Chúng tôi cung cấp các máy SMT với công nghệ tự động giúp doanh nghiệp hoàn thiện hơn quá trình sản xuất thông minh, TPA sẵn sàng trở thành nhà cung cấp giải pháp về máy SMT, dây chuyền SMT, dây chuyền sản xuất bảng mạch cho các nhà máy ngành điện – điện tử, ô tô, thiết bị điện…Tham khảo ngay Catalogue sản phẩm của chúng tôi dưới đây:
XEM THÊM:
►Dây chuyền sản xuất tự động là gì? Lợi ích của tự động hóa trong sản xuất
—————————————————————–
MỌI THÔNG TIN CHI TIẾT LIÊN HỆ
CÔNG TY CỔ PHẦN GIẢI PHÁP TỰ ĐỘNG HÓA ETEK
Từ ngày 14/6/2022, Công ty Cổ phần Tự động hoá Tân Phát (TPA) chính thức có tên gọi là ETEK
Địa chỉ trụ sở chính 189 Phan Trọng Tuệ –Thanh Liệt- Thanh Trì – Hà Nội
Hotline: (+84) 965.800.166
Hoặc để lại thông tin tại Boxchat
Website: tpa.com.vn, tpaparking.vn , tpad.vn , tpa-fas.com.vn
PCB magazine rack – Quang Minh ist co.,ltd
1. Giá đựng bảng mạch SMT ( PCB magazine rack) là gì?
Giá đựng bảng mạch SMT hay còn gọi là Giá để bản mạch PCB magazine rack là một trong những thiết bị không thể thiếu trong ngành công nghiệp sản xuất SMT (Surface Mount Technology – Công nghệ dán bề mặt), một ngành công nghiệp đang rất phát triển trong những năm qua đặc biệt tại Việt Nam
Giá đựng bo mạch SMT PCB magazine rack là thiết bị dùng để đựng, chứa, lưu trữ các bảng mạch PCB, FPCB trong quá trình sản xuất, vận chuyển tránh các va đập vật lý, các phản ứng hóa học hay đặc biệt là hiện tượng tĩnh điện có thể gây tổn hại đến các tụ điện các tụ điện trên mạch điện bán dẫn.
2. Chức năng của giá đựng bảng mạch PCB magazine rack
Giá đựng bản mạch chống tĩnh điện PCB magazine rack có chức năng chính đó là sắp xếp các bảng mạch PCB được đúng trật tự trong quá trình sản xuất, vận chuyển cũng như lưu trữ, cũng như giúp công nhân sản xuất có thể sắp xếp phân loại dễ dàng hơn tránh nhầm lẫn trong quá trình gia công mạch PCB và FPCB
3. Vai trò của giá đựng bản mạch PCB magazine rack trong sản xuất SMT
Giá để bảng mạch có một vai trò cực kì quan trọng trong các nhà máy sản xuất SMT ngày nay.
Giá đỡ bảng mạch có vai trò chống va đập gây cong vênh cho các bản mạch PCB hay FPCB. Các giá đựng bản mạch cũng phải có khả năng chống tĩnh điện để bảo vệ các vật liệu bán dẫn và các tụ điện để không gây ra những hư hại không đáng có trong trường hợp tích điện xảy ra mà những nơi lưu trữ không có dây tiếp nối đất.
Trong quá trình lưu trữ và vận chuyển các bản mạch thì các giá để bản mạch còn có một vai trò rất quan trọng đó chính là tiết kiệm không gian lưu trữ. Với thiết kế đặc biệt của tùy từng loại giá mà có thể tiết kiệm từ 15 đến 25% không gian. Từ đó tiết kiệm chi phí kho bãi cũng như vận chuyển cho nhà sản xuất.
Các mỗi hàn thiếc trên mạch bán dẫn PCB hay FPCB thường có khả năng chịu nhiệt kém. Do đó các giá để bản mạch còn có vai trò như một thiết bị cách nhiệt bảo vệ các mối hàn trên mạch được an toàn khi đi qua các nơi có nhiệt độ cao, hạn chế tối đa các lỗi về mối hàn trên bảng mạch không đáng có.
4. Các loại giá để bản PCB magazine rack mạch thông dụng thường được sử dụng
Giá để bản mạch PCB magazine rack thông thường được chia ra làm nhiều kích thước để tùy phục vụ mỗi nhu cầu sử dụng của nhà sản xuất như
5. Cấu tạo giá đựng bảng mạch PCB magazine rack
Tùy từng sản phẩm mà cấu tạo của giá đựng bảng mạch có từng cấu tạo khác nhau. Tuy nhiên về cơ bản các giá để bo mạch có cấu tạo cơ bản như sau:
Tấm đáy: là nơi được dùng để cố định các chi tiết khác nhau của giá đỡ bản mạch
Các thanh đỡ chịu lực: được dùng để cố định vf chịu lực tại các góc của giá đỡ bảng mạch
Tấm vách: là nơi lắp đặt các khe để bảng mạch
Thanh chặn: dùng để chặn các bảng mạch rơi ra và đảm bảo cho việc đưa bảng mạch vào từ 1 hướng duy nhất
Tấm vách di động: dùng để cố định và sắp xếp các bảng mạch
Ngoài ra tùy vào từng sản phẩm mà có thể sẽ có những thay đổi về mặt cấu tạo. Tuy nhiên về cơ bản cấu tạo của một giá đựng bảng mạch đều bao gồm các thành phần trên.
Nếu quý khách có nhu cầu mua giá để bản mạch hãy gọi ngay cho chúng tôi
CÔNG TY TNHH KỸ THUẬT VÀ DỊCH VỤ CÔNG NGHIỆP QUANG MINH
⇨ Hotline : 0987 935 898
⇨ Điện thoại : 0225 710 88 99
⇨ Email: [email protected]
Surface Mount (SMT) PCB Assembly Manufacturer- JLCPCB
Hands-off Sourcing
JLCPCB have 350k+ Components In-stock. You don’t have to worry about parts sourcing, this helps you to save time and hassle, also keeps your costs down.
Moreover, you can pre-order parts and hold the inventory at JLCPCB, giving you peace-of-mind that you won’t run into any last minute part shortages.
Explore JLCPCB Parts Library →
Tìm Hiểu Chi Tiết Về Công Nghệ Dán Bề Mặt SMT
By Lidin Co 576 view
Công nghệ dán bề mặt SMT với những ưu điểm nổi trội về tính tự động hóa và hiệu suất cao được ứng dụng rộng rãi trong lĩnh vực sản xuất bảng mạch in PCB. Cùng tìm hiểu các thông tin chi tiết về công nghệ SMT và các loại máy SMT không thể thiếu trong quy trình.
SMT Là Gì?
Công nghệ SMT (viết tắt của surface mount technology) còn được gọi là công nghệ dán bề mặt trong đó linh kiện điện được gắn dán trực tiếp trên bề mặt của mạch in (PCB hay còn gọi là printed circuit board).
Một linh kiện điện tử được dán theo cách này thì được gọi là linh kiện dán (SMD hay surface mount device). Công nghệ SMT đã thay thế phần lớn công nghệ xuyên lỗ để lắp đặt các linh kiện điện nhờ khả năng tự động hóa cao. Giúp giảm chi phí và cải thiện chất lượng sản phẩm. Công nghệ SMT cũng cho phép lắp đặt nhiều linh kiện có kích thước khác nhau vào một khu vực bảng mạch nhất định.
Ưu Nhược Điểm Của Công Nghệ Dán Bề Mặt SMT:
Ưu Điểm:
Đáp ứng nhu cầu về các thành phần, linh kiện điện tử ngày càng có kích thước nhỏ hơn.
Mật độ thành phần, linh kiện cao hơn giúp kết nối các thành phần trong bảng mạch hiệu quả hơn. Vì các lỗ không chặn không gian định tuyến trên các lớp, cũng như trên mặt sau của bảng mạch nếu các thành phần chỉ được gắn trên một mặt của PCB.
Các thành phần linh kiện điện tử có thể được dán ở cả hai mặt của bảng mạch in PCB
Hiệu suất cơ học tốt hơn trong điều kiện va đập và rung động
Điện trở và điện cảm thấp hơn. Do đó, ít hiệu ứng tín hiệu RF không mong muốn và hiệu suất tần số cũng cao và dễ đoán hơn.
Hiệu suất điện từ (phát xạ bức xạ) tốt hơn do diện tích vòng bức xạ nhỏ hơn và điện cảm dẫn ít hơn.
Số lỗ cần khoan ít hơn. (Khoan PCB tốn nhiều thời gian và chi phí)
Khả năng tự động hóa cao, giảm thiểu được chi phí nhân công và thời gian sản xuất
Lắp ráp tự động đơn giản và nhanh chóng hơn. Một số máy định vị có khả năng đặt hơn 136.000 linh kiện mỗi giờ.
Nhược Điểm:
Công nghệ SMT trong một số trường hợp có thể không phù hợp để gắn các thành phần chịu ứng suất cơ học thường xuyên. Ví du như các đầu nối được sử dụng để giao tiếp với các thiết bị bên ngoài thường được gắn tách rời.
Các mối hàn SMD cần kiểm tra kĩ bằng máy chuyên dụng vì lỗi nhỏ khó phát hiện bằng mắt thường.
Các thành phần linh kiện SMD thường có kích thước nhỏ và cần các dụng cụ chuyên dụng để xử lý.
Chi phí để mua máy móc và thiết bị ban đầu tốn kém hơn.
Công đoạn phát hiện và sửa chữa lỗi cần đầu tư kĩ lưỡng.
Một Số Thuật Ngữ Thường Gặp:
Khi tìm hiểu về công nghệ SMT, bạn sẽ bắt gặp rất nhiều các thuật ngữ viết tắt như SMD, SMC, SME. Vậy chúng có ý nghĩa là gì. Hãy cùng tìm hiểu nhé:
Viết tắt Ý nghĩa SMD SMD là linh kiện dán bề mặt. Viết tắt của surface-mount devices (ở đây có thể là linh kiện thụ động, chủ động hoặc cơ điện) SMT SMT là công nghệ dán bề mặt. Viết tắt của surface mount technology. SMA SMA là lắp ráp bề mặt. Viết tắt của surface mount assembly SMC SMC là thành phần dán bề mặt. Viết tắt của surface mount components SME SME là thiết bị dán bề mặt. Viết tắt của surface-mount equipment. PCB PCB là bảng mạch in. Viết tắt của từ printed circuit board.
Quy Trình SMT Bao Gồm Các Giai Đoạn Nào?
Thiết kế board mạch:
Bước đầu tiên của quy trình SMT là thiết kế các bảng mạch in điện tử. Sử dụng phần mềm giúp lựa chọn và sắp xếp vị trí các linh kiện đồng thời định tuyến để xác định kết nối điện trên bảng mạch. Cho ra sơ đồ và chế bản điện tử thuận tiện cho các bước tiếp theo. Một số phần mềm được sử dụng như Orcad hoặc Cadstar. Ngoài ra còn có các phần mềm EDA và CAD chuyên dụng khác để xử lý tùy biến.
Lựa chọn linh kiện:
Sau khi được thiết kế, bản vẽ mạch in PCB sẽ được gửi tới các công ty sản xuất PCB và linh kiện điện tử để đặt hàng. Bảng mạch in sẽ được thực hiện khoan cắt và định vị vị trí. Còn linh kiện sẽ được cung cấp theo yêu cầu. Các thành phần linh kiện điện tử thường được đóng gói bằng nhiều cách khác nhau theo cuộn, ống hoặc trong khay.
Do thành phần linh kiện có kích thước nhỏ nên bước đầu để kiểm soát số lượng đầu vào sẽ cần đếm bằng cách thủ công hoặc sử dụng máy đếm linh kiện như bên dưới để tiết kiệm công sức và đạt hiệu quả cao hơn:
Sau đó linh kiện sẽ được sắp xếp lên các line sản xuất để chuẩn bị cho quá trình lắp ráp tiếp theo.
Giai đoạn lập trình máy tự động:
Sau khi đã có đầy đủ linh kiện điện tử và bảng mạch PCB cần thiết. Bước tiếp theo chuẩn bị cài đặt và lập trình các máy móc liên quan. Ưu điểm rất lớn của công nghệ SMT là khả năng tự động hóa cao. Các loại máy móc được cài đặt sẵn để lắp ráp, sửa chữa, phát hiện lỗi theo quy trình tự động. Đảm bảo tối ưu hóa hiệu suất và giảm chi phí cho doanh nghiệp.
Các loại máy như máy gắp đặt linh kiện dán SMD và máy kiểm tra lỗi quang học AOI sẽ cần thiết lập từng vị trí cụ thể theo tọa độ. Trong đó các phần mềm chuyên dụng sẽ chuyển đổi dữ liệu Gerber/ CAD thành file Centroid và vị trí tọa độ XY.
Công đoạn quét kem hàn:
Tại giai đoạn này, máy quét kem hàn được sử dụng để quét kem hàn lên bảng mạch PCB. Máy sử dụng dao gạt để quét kem hàn lên các tấm bảng mạch PCB đã được đục sẵn lỗ.
Giai đoạn kiểm tra kem hàn SPI (Solder Paste Inspection):
Tuy quy trình quét kem hàn nghe qua khá đơn giản nhưng thường sẽ có nhiều lỗi phát sinh nếu không được xử lý cẩn thận áp lực của dao gạt và lượng kem hàn cần thiết. Bên cạnh đó, giai đoạn kiểm tra SPI còn giúp phát hiện sớm và giảm thiểu rủi ro do các lỗi gây ra.
Thường thì các máy quét kem hàn tự động solder paste printer sẽ có kèm tính năng kiểm tra 2D. Tuy nhiên có những lỗi khó phát hiện được mà phải cần đến máy SPI để kiểm tra bề mặt 3D của từng miếng đệm (pad) riêng biệt.
Một số lỗi liên quan đến kem hàn thường gặp
Gắp đặt thành phần linh kiện:
Sau khi bảng mạch in PCB đã được quét đủ lượng kem hàn. Nó sẽ được di chuyển tới giai đoạn tiếp theo của quá trình SMT là gắp đặt thành phần linh kiện. Mỗi loại linh kiện sẽ được lấy ra tự động bằng đầu hút chân không hoặc kẹp gắp, di chuyển tới vị trí đã được thiết lập sẵn trên hệ thống và đặt chính xác tại đó với tốc độ cao.
Các công đoạn xử lý của máy gắp đặt thành phần linh kiện thường sẽ bao gồm:
Lập chỉ mục bảng (board indexing)
Thiết lập bảng (board registration(
Điều chỉnh tầm nhìn fiducial (fiducial vision alignment)
Gắp linh kiện (component pick-up)
Định vị các thành phần linh kiện / kiểm tra tầm nhìn (component centering/ vision inspection)
Đặt các thành phần, linh kiện điện tử và đúng các vị trí đã lập chỉ mục trên bảng mạch
Kiểm tra quang học tự động (automated optical inspection)
Kiểm tra trước khi hàn reflow (Pre-reflow Automated Optical Inspection):
Sau giai đoạn lắp đặt linh kiện, để đảm bảo mọi thành phần đều đã được đặt chính xác trước khi cho bảng mạch PCB tiến tới bước hàn reflow, người ta sẽ kiểm tra trước khi hàn bằng máy AOI. Một số lỗi quan trọng như vị trí, thành phần, mật độ và thiếu sót linh kiện sẽ được kiểm tra kĩ càng.
Giai đoạn hàn Reflow:
Tiếp theo, bảng mạch PCB sẽ được đưa vào lò hàn reflow. Phần kem hàn dưới tác động của nhiệt lượng sẽ nóng chảy tạo ra các mối hàn gắn chặt linh kiện lại trên bảng mạch. Sẽ có từng giai đoạn nhiệt độ riêng biệt để các mối hàn được nóng chảy đủ mà không làm hư hại đến các thành phần linh kiện trong đó.
Sau giai đoạn làm nóng sẽ đến giai đoạn hạ nhiệt và làm sạch để loại bỏ các kèm hàn dư sót lại.
Quy trình nhiệt hàn reflow:
Vùng preheat: độ tăng nhiệt độ cao nhất là 2.5 độ C / s ở khu vực làm nóng. Sự tăng nhiệt quá đột ngột có thể dẫn đến lỗi bóng hàng (solder balling)
Vùng ngâm nhiệt( soak zone): là vùng giữ nhiệt độ trong khoảng 150-210 độ C. Mức tăng nhiệt độ không quá 2.5 độ C/s suốt vùng ngâm nhiệt. Giai đoạn này thường kéo dài 60-90s
Vùng reflow: là giai đoạn đạt được nhiệt độ đỉnh. Trong vùng hàn reflow nhiệt độ thay đổi trong khoảng 230-255 độ C và nhiệt độ trên 217 độ C được giữ trong 40-70s.
Vùng hạ nhiệt (cool-down zone): nhiệt độ sẽ được hạ xuống tại vùng này và độ giảm nhiệt sẽ hạ khoảng 4 độ C/s
Kiểm tra AOI:
Sử dụng thiết bị kiểm tra bề mặt(visual inspection) tự động của bảng mạch in (PCB), LCD hoặc transistor. Trong đó một camera tự động quét thiết bị đang được kiểm tra để phát hiện các lỗi liên quan như thiếu linh kiện, sai linh kiện, sai lệch vị trí, kích thước hoặc hình dạng của linh kiện so với thiết kế ban đầu. Ngoài ra máy AOI có thể được kết nối với máy định vị để dễ dàng điều chỉnh các vị trí đặt linh kiện và sửa chữa khi có lỗi.
Kiểm tra X-ray:
AXI là công nghệ sử dụng nguyên tắc tương tự như kiểm tra quang học (AOI). Tuy nhiên nó sử dụng tia X-ray thay vì tia sáng quang học để tự động kiểm tra các thành phần linh kiện. Máy AXI không chỉ có khả năng kiểm tra các mối hàn và các lỗi khuyết tật có thể nhìn thấy được mà còn có khả năng kiểm tra các mối nối hàn ở các vị trí khó phát hiện hoặc các lỗi bị che khuất.
Các loại máy SMT cần thiết:
Công nghệ dán bề mặt SMT đòi hỏi trình độ kĩ thuật và đầu tư máy móc chất lượng cao. Tại Việt Nam, công ty Lidinco chuyên phân phối và cung cấp các loại máy SMT phục vụ cho dây chuyền sản xuất, gia công, lắp ráp bảng mạch PCB chính hãng, hỗ trợ kỹ thuật và chuyên môn. Liên hệ ngay để được tư vấn miễn phí:
Công Ty TNHH Đầu Tư Phát Triển Cuộc Sống
Địa chỉ: 487 Cộng Hòa, Phường 15, Quận Tân Bình, TPHCM, Việt Nam
Điện thoại: 028 3977 8269 / 028 3601 6797 / 028 3977 8019
Email: [email protected]
키워드에 대한 정보 smt pcb & nepcon korea 2019
다음은 Bing에서 smt pcb & nepcon korea 2019 주제에 대한 검색 결과입니다. 필요한 경우 더 읽을 수 있습니다.
이 기사는 인터넷의 다양한 출처에서 편집되었습니다. 이 기사가 유용했기를 바랍니다. 이 기사가 유용하다고 생각되면 공유하십시오. 매우 감사합니다!
사람들이 주제에 대해 자주 검색하는 키워드 Quy trình sản xuất SMT – SMT PCB Assembly Process
- smt
- smt process
- sms
- panasonic
- yamaha
- saki
Quy #trình #sản #xuất #SMT #- #SMT #PCB #Assembly #Process
YouTube에서 smt pcb & nepcon korea 2019 주제의 다른 동영상 보기
주제에 대한 기사를 시청해 주셔서 감사합니다 Quy trình sản xuất SMT – SMT PCB Assembly Process | smt pcb & nepcon korea 2019, 이 기사가 유용하다고 생각되면 공유하십시오, 매우 감사합니다.